But there is also time for everybody to come take a peek at one last alternative fuel vehicle -- this one a SVO (Straight Vegetable Oil) conversion, or "greasecar." This 2005 Volkswagen Jetta TDI gets over 40 mpg gallon on diesel fuel -- and the same on used and filtered vegetable oil. Owner Bob spent the whole morning with us so that folks could come out, admire and ask questions instead of twiddling their thumbs between assignments or while waiting for another task group to complete their work. We are very grateful to Bob for his generous, impromptu visit, and to Stan of NMTCC for arranging it!
This is the tank for the used veggie oil, neatly installed in the former spare tire compartment in the trunk.
On the left above is the original diesel filter. and in the foreground the installed filter for the veg oil. A greasecar begins running on diesel, then switches to SVO when the engine reaches the proper temperature. Thus, they're ideal for people who do a lot of driving at a time, and less suitable for those who have limited commutes. The perfect long-range complement to an EV!
For more information visit Greasecar Vegetable Fuel Systems.
Bill is dying to put one of these into his diesel Benz, and the two of us have been dreaming for a little while about putting on a workshop on that process. Stay tuned--and email me if you have an interest so I can send you an announcement directly if & when this idea comes to fruition!
Meanwhile, back on the van, Rudy gets his first crimping lesson ...
from start to finish.
John also gets a chance to crimp while JJ and Bill ponder wiring issues in the background.
Paul's wiring up the speedometer, which had come unhooked somehow (so there was a little bit of hands-on work behind the dashboard after all!).
Now things are moving into high gear as the rear battery racks are mounted and the batteries installed.
Completed batteries in their battery racks.
For a while it looked like we might have to re-engineer some of the hold-downs, because some of the tabs had been installed backwards and there wasn't quite enough clearance for the passenger seat to latch. There was talk of making longer bolts, and my heart sank at the thought of another round of fabricating, welding and waiting for paint to dry. No way would the van roll by 4 if that had to happen! Instead Bill proposed an ingenious short-cut: make holes in the back of the seat to accommodate the battery racks. That was quick and easy, and it did the job, so whew!
Now Paul could move on to torquing down the washers on the batteries ...
and Rob and Vincent could begin wiring up the connections.
Everything began moving fast (above, wrapping orange electrical tape around the conduit sleeving for the long cable that will connect rear batteries to front batteries).
After the overview of components, the safety check began. Following the steps outlined in our "bible," Bob Batson's EVAmerica conversion manual, Leo checked the voltages at each major connection.
With the safety checklist completed, we were ready to power up and test the main contactor and then the throttle linkage. This, of course, needs to be done with the van lifted off the ground, so up she went on the lift. When the key turned in the ignition, the contactor opened -- but when the accelerator was pressed, nothing happened. No controller whine, no wheels turning. Oh no! And look what time it was!
Everything began moving fast (above, wrapping orange electrical tape around the conduit sleeving for the long cable that will connect rear batteries to front batteries).
Meanwhile (and I have no pictures of this because I was too busy panicking) we had to weather a small crisis with the auxiliary DC battery. First Bill and Paul told me it didn't work and we would need to wait half an hour for a new Vanagon battery to get here from the auto parts delivery store. This turned out to be a joke -- ha ha, but with not even two hours left on the clock, it was too scary to be very funny to me! Then, guess what -- the working, but not-properly-sized for a Vanagon battery turned out to be the wrong size for the battery compartment.
There was some concern about stretching of cables and whether we'd be able to close the top of the compartment (we couldn't). At this point I blush to admit that I was so worried we wouldn't roll that I burst into tears! Everything depends on the DC battery, since without it the main contactor won't open. But I was reassured the e-Van could roll and we could safely test it with this temporary set-up.
I was incredibly relieved, though I was still sniffling a little when Leo gathered the class (plus a group of summer campers from NMTCC) to explain to everybody how all the major components of the EV system work together to make the vehicle go. It was an exceptionally lucid and educational review; Rob took a video of the whole thing, which I hope to post a link to on this site soon. Note from the future: you can watch it here
With the safety checklist completed, we were ready to power up and test the main contactor and then the throttle linkage. This, of course, needs to be done with the van lifted off the ground, so up she went on the lift. When the key turned in the ignition, the contactor opened -- but when the accelerator was pressed, nothing happened. No controller whine, no wheels turning. Oh no! And look what time it was!
I managed not to have a meltdown while the diagnostic scurry took place. In surprisingly short order it was established that actually, one of the long high-voltage cables had been installed backwards. (There had been some debate about whether to innovate on this aspect of the wiring because we'd switched the battery configuration around, or follow Bob Batson's original schematic -- in the end, Bob Batson was right! That's what we get for not following the bible!)
Bill informed me afterwards that we were very, very lucky that we didn't blow the controller. All that happened was that nothing happened -- much, much better than a pop and smoke, and the loss of a $1500 EV component! Not to mention that that would have put an end to our hopes of getting the van to roll ...
With the cable swapped around (and, incidentally, the proper Vanagon battery installed), Paul got the honor of turning the key on the second test. Key on, contactor open. Press down on the throttle and YES! The controller whined and the wheels turned!
Bill informed me afterwards that we were very, very lucky that we didn't blow the controller. All that happened was that nothing happened -- much, much better than a pop and smoke, and the loss of a $1500 EV component! Not to mention that that would have put an end to our hopes of getting the van to roll ...
With the cable swapped around (and, incidentally, the proper Vanagon battery installed), Paul got the honor of turning the key on the second test. Key on, contactor open. Press down on the throttle and YES! The controller whined and the wheels turned!
This van wants to be electric -- but she also seems to want to get there at the last possible minute!
After a parting toast with non-alcoholic champagne and handing out of completion certificates, EV Conversion Workshop 2009 came to an official close with hugs, handshakes and farewells. This was really an amazing group of people who came together for a week to undertake a challenging project, worked together to solve countless difficulties under time pressure, and somehow managed to keep it all friendly, positive and fun! I am so grateful to Bill for leading us all through the process and to all the participants for their tremendous contributions.
Thanks for following along!
Bill backed the e-Van off the lift and out of the shop and took her for her first spin around the parking lot, and then everybody got to drive her. Check out all the EV grins in the photo collage below! I was so wobbly with relief that I didn't get shots of everyone behind the wheel but I hope class members will send them in (along with any video) so I can post them.
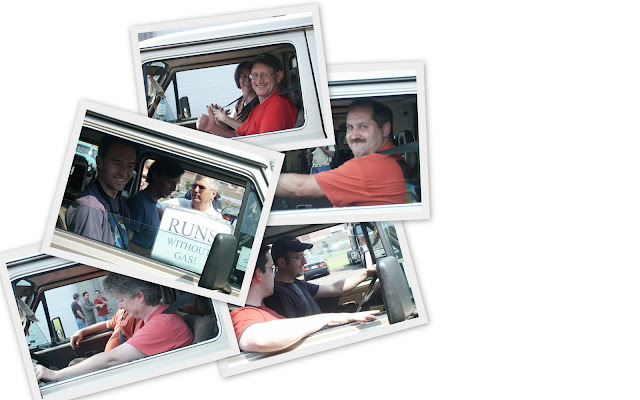
There's a lot left to tidy up on the e-Van, of course. Leo sent a detailed list of the loose ends that need to be attended to in the wiring department -- and we still need to build battery boxes so that the batteries are safely enclosed. Bill and I are also hoping to give the van a paint job and spruce up the interior before show time at the PA Energy Fest in Kempton, PA September 18, 19, and 20!
Hope to see you there -- and in the meantime, I'll post regular updates on our progress and on the performance benchmarking. The rebuilt e-Van certainly feels speedier and more powerful, and an hour of testing didn't drop the battery-charge indicators at all -- but we'd like to get some numbers on our range and see if we've achieved our 50-mile goal!
Thanks for following along!